Comprehensive Overview: What is Porosity in Welding and Just How to Prevent It
Comprehensive Overview: What is Porosity in Welding and Just How to Prevent It
Blog Article
The Science Behind Porosity: A Comprehensive Overview for Welders and Fabricators
Understanding the elaborate devices behind porosity in welding is essential for welders and makers making every effort for impeccable workmanship. From the composition of the base materials to the intricacies of the welding process itself, a plethora of variables conspire to either worsen or reduce the presence of porosity.
Comprehending Porosity in Welding
FIRST SENTENCE:
Exam of porosity in welding exposes important insights right into the honesty and quality of the weld joint. Porosity, characterized by the presence of cavities or gaps within the weld metal, is a common concern in welding procedures. These voids, if not properly resolved, can endanger the architectural stability and mechanical homes of the weld, resulting in potential failures in the ended up item.
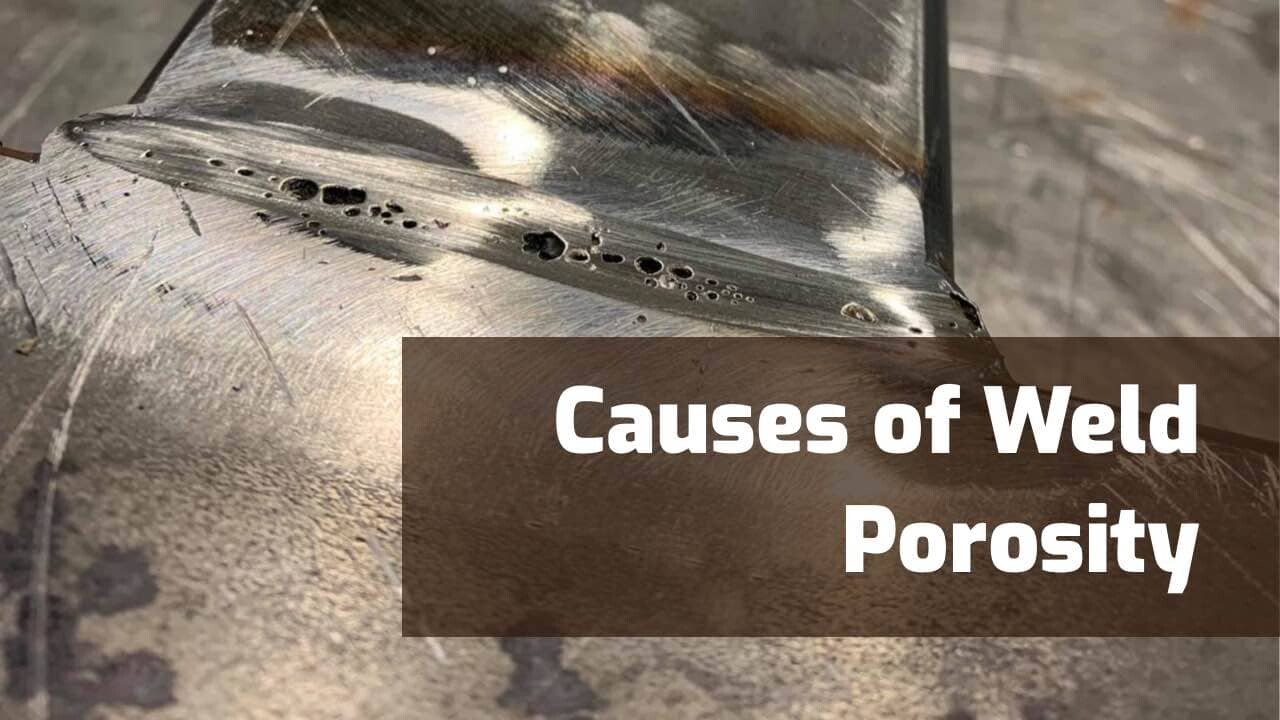
To find and measure porosity, non-destructive testing methods such as ultrasonic testing or X-ray evaluation are commonly utilized. These techniques permit the recognition of inner flaws without jeopardizing the integrity of the weld. By examining the size, form, and circulation of porosity within a weld, welders can make educated decisions to enhance their welding processes and attain sounder weld joints.

Factors Affecting Porosity Development
The incident of porosity in welding is influenced by a myriad of variables, ranging from gas securing efficiency to the details of welding parameter settings. Welding specifications, consisting of voltage, present, take a trip rate, and electrode kind, also impact porosity development. The welding technique utilized, such as gas steel arc welding (GMAW) or secured steel arc welding (SMAW), can affect porosity formation due to variations in warm circulation and gas coverage - What is Porosity.
Effects of Porosity on Weld High Quality
Porosity development dramatically compromises the structural stability and mechanical residential properties of bonded joints. When porosity is existing in a weld, it develops gaps or dental caries within the material, decreasing the general toughness of the joint. These voids act as tension focus factors, making the weld more vulnerable to splitting and failure under load. The presence of porosity also compromises the weld's resistance to rust, as the caught air or gases within the voids can react with the surrounding setting, causing deterioration gradually. Furthermore, porosity can impede the weld's capability to withstand pressure or influence, more endangering the overall quality and special info reliability of see this website the welded structure. In critical applications such as aerospace, automobile, or structural building and constructions, where security and longevity are vital, the harmful impacts of porosity on weld high quality can have serious consequences, stressing the importance of reducing porosity through correct welding strategies and treatments.
Techniques to Lessen Porosity
Furthermore, using the suitable welding specifications, such as the right voltage, present, and take a trip rate, is critical in preventing porosity. Keeping a regular arc size and angle throughout welding additionally helps reduce the probability of porosity.

Moreover, picking the ideal securing gas and maintaining appropriate gas circulation prices are crucial in minimizing porosity. Making use of the suitable welding method, such as back-stepping or utilizing a weaving movement, can likewise aid distribute heat equally and minimize the possibilities of porosity development. Making sure appropriate ventilation in the welding setting to get rid of any type of prospective sources of contamination is important for achieving porosity-free welds. By implementing these strategies, welders can efficiently minimize porosity and produce high-grade bonded joints.

Advanced Solutions for Porosity Control
Carrying out sophisticated innovations and cutting-edge techniques plays a crucial duty in accomplishing remarkable control over porosity in welding procedures. Additionally, using advanced welding techniques such as pulsed MIG welding or changed atmosphere welding can additionally assist alleviate porosity concerns.
Another sophisticated remedy includes making use of advanced welding tools. Using equipment with integrated attributes like waveform control and advanced power sources can enhance weld quality and decrease porosity dangers. Moreover, the implementation of automated welding systems with specific control over criteria can dramatically minimize porosity defects.
Furthermore, incorporating advanced surveillance and examination modern technologies such as real-time X-ray imaging or automated ultrasonic screening can assist in finding porosity early in the welding process, enabling immediate rehabilitative activities. Overall, integrating these advanced remedies can significantly enhance porosity control and enhance the overall top quality of bonded elements.
Verdict
To conclude, comprehending the scientific research read this post here behind porosity in welding is crucial for welders and makers to generate high-quality welds. By determining the factors affecting porosity development and implementing strategies to reduce it, welders can enhance the overall weld quality. Advanced remedies for porosity control can better improve the welding process and make certain a solid and dependable weld. It is necessary for welders to continually inform themselves on porosity and execute ideal techniques to accomplish optimal results.
Report this page